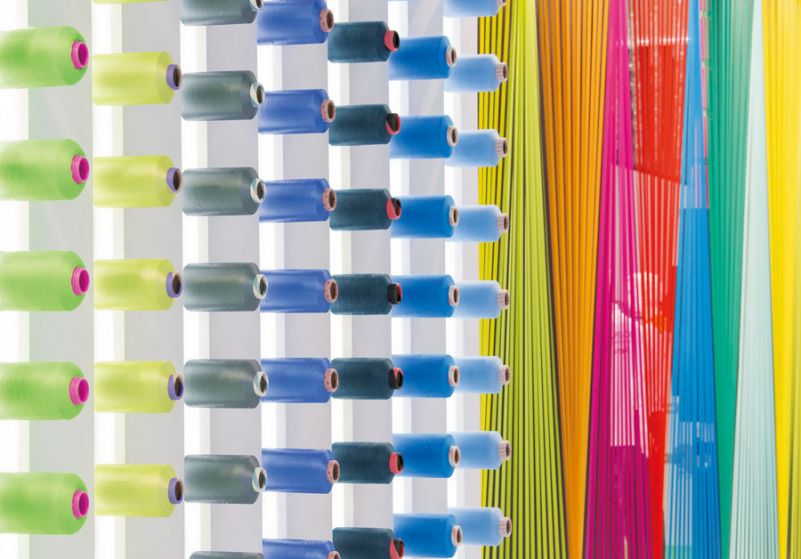
Products showcased at the 2017 Taipei Innovative Textile Application Show held Oct. 16-18 (Photo by Chin Hung-hao)
When it comes to innovative products, consumers rarely think of the shirts on their backs. But any preconceived notions about a lack of technological sophistication in the textiles industry would be quickly dispelled by a visit to the textured yarn factory operated by Lealea Enterprise Co., an affiliate of Libolon Group, in central Taiwan’s Changhua County. Located at Fangyuan Industrial Park, the facility hosts 28 texturing machines producing 2,200 tons of yarn a month, all monitored from a centralized control hub.
Reaching this level of efficiency required a steadfast commitment to innovation. “As early as 1996, we began pioneering automated processes spanning the entire production chain,” said Chen Han-ching (陳漢卿), spokesperson for Taipei City-based Libolon. “Back in those days, corporate representatives from more than 20 countries visited the plant to learn about our advances.”
The factory’s newest improvements are likely to have overseas delegations beating down the doors once again. Completed in 2016, they significantly boost efficiency by incorporating cutting-edge solutions in such fields as big data analysis, Internet of Things and smart manufacturing.
|
Lealea’s latest modifications were planned and financed under the Taiwan Productivity 4.0 Initiative, a government program launched in 2015 to promote the adoption of Industry 4.0 technologies throughout the manufacturing sector. The upgrades were subsidized by the Industrial Development Bureau (IDB) under the Ministry of Economic Affairs and guided by two government-supported research organizations, the Institute for Information Industry and Taiwan Textile Research Institute. To date, the textured yarn-maker is one of 10 companies to have benefited from the program aimed at showcasing the advantages and potential applications of digitally integrated production.
Economic Pillar
The plant’s inclusion in the Taiwan Productivity 4.0 Initiative spotlights the significance of the textiles sector, long a pillar of the nation’s economy. According to the Taiwan Textile Federation (TTF), the country was home to 4,361 textiles companies employing more than 142,000 people in 2016, the latest year for which statistics are available. These firms span the entire supply chain from upstream man-made fiber producers to downstream apparel-makers. Midstream fabric manufacturing is the largest industry segment, accounting for about two-thirds of exports in terms of value.
TTF data show that total sector production value reached about NT$390 billion (US$13 billion) in 2016, with Taiwan ranking seventh globally in exports. Textiles also generated the fourth largest trade surplus among local industries that year at US$6.58 billion, according to the federation. “Though we face increasingly fierce competition worldwide, the country has remained a major player because of firms’ integrity,” TTF President Justin Huang (黃偉基) said. “Enterprises keep their promises to clients, even if it means making a loss.”
|
According to Huang, innovation and upgrading are the other key elements in the success of local companies. Due to consistent industrywide investment in R&D, Taiwan is the world’s leading source of functional fabrics. Regular improvements in production processes and technologies have also helped firms remain at the forefront of two major trends: smart manufacturing and sustainability. “No industry player can afford to ignore environmental issues,” he said. “Nowadays, virtually all major global brands want their products to convey an eco-friendly image to consumers.”
Sustainable Solutions
Efforts to introduce environmentally friendly production practices have mainly targeted dyeing, since traditional coloring processes require large amounts of water and generate significant effluent discharges. To reduce pollution, Taiwan companies have embraced a variety of greener methods, including solution and supercritical carbon dioxide dyeing, as well as digital textile printing.
An industry leader in sustainable approaches, Libolon created its own brand Ecoya in 2006 for yarns colored using solution dyeing, a technique that consists of adding hues to synthetic fibers while they are still in a liquid state. Chen said that the yarns, the product of more than two years of R&D, require about 90 percent less water to dye compared with regular processes, which involve dipping fabrics into pigments.
|
Taipei-based Far Eastern New Century Corp. (FENC), another leader in eco-friendly solutions, has pioneered supercritical CO2 dyeing at a plant co-established with U.S. apparel firm Nike Inc. in northern Taiwan’s Taoyuan City. This technique employs pressurized recycled CO2 instead of water in the production process. In addition to completely eliminating water use, it reduces the amount of dye needed by about two-thirds in comparison with conventional practices.
Local firms have also embraced recycling in an effort to lower their environmental footprint. Libolon collects used clothes from consumers through its 11 Go Hiking outerwear stores in Taiwan. It then transforms them into plastic chips that can be mixed with waste wood powder to make construction materials. The conglomerate is also among a number of local manufacturers producing textiles from discarded polyethylene terephthalate, or PET, bottles.
According to FENC, Taiwan boasts the world’s highest PET bottle recycling rate at about 95 percent, and nearly half of all these containers end up in its plants. The company commenced research on recycled PET textiles in 1988 and has since developed mature technologies in such areas as chip production, dyeing, flake grinding and knitting. Owing to its expertise in this field, FENC was contacted by Adidas in 2015 after the Germany-headquartered clothing company established a partnership with New York-based nongovernmental organization Parley to tackle the buildup of plastic waste in the world’s oceans. Under the three-way venture, the Taiwan textile firm turns PET bottles collected from beaches in the Indian Ocean into Adidas products like running shoes and jerseys.
International Outreach
Growing international recognition of Taiwan’s expertise in eco-friendly production methods and functional fabrics is reflected in the popularity of the annual Taipei Innovative Textile Application Show. Staged last October, the 21st edition of the TTF-organized event attracted a record 383 companies from around the world. Taiwan is also enhancing ties with overseas businesses through the Textile Industry Promotion Office (TIPO), a government unit launched in 2008 under the IDB to boost cooperation and exchanges between state-run agencies, local industry players and research organizations.
|
The office is currently developing an initiative aimed at fostering collaboration between Taiwan firms and their foreign counterparts, particularly those in Southeast Asia. Under the plan, TIPO has assembled a technical services unit that will offer expert guidance to businesses in the region. This new division, which will be supported by an advisory group consisting of academic, private and public sector representatives, is expected to commence work later this year in Malaysia. These efforts are in line with the New Southbound Policy, a key plank in the government’s national development strategy that seeks to promote Taiwan’s agricultural, business, cultural, education, tourism and trade ties with the 10 Association of Southeast Asian Nations member states, six South Asian countries, Australia and New Zealand.
“We’ll conduct comprehensive business process surveys for companies so we can help them determine which areas require the most attention and resource investment,” said Chen Chin-lai (陳進來), TIPO deputy executive manager. “We’re also going to work with them on talent cultivation.” These technical assistance projects will produce significant mutual benefits through increased demand for Taiwan products such as dyes and equipment, he added.
Greater integration of regional supply chains is set to further strengthen Taiwan’s status as a hub of textile innovation. At a Lealea polyester fiber factory, also located in Fangyuan Industrial Park, Chang Chun-ching (張春景) highlighted a newly introduced machine for stringing up yarns and sending them to bobbins, the least automated part of the plant’s production process. The Lealea vice president said the company plans to install more of the machines, among the most advanced of their kind in the world, over the next several years. “We’ve attained a leading position in the global industry,” Chang said. “But we also recognize we must constantly prepare for and embrace the latest developments.”