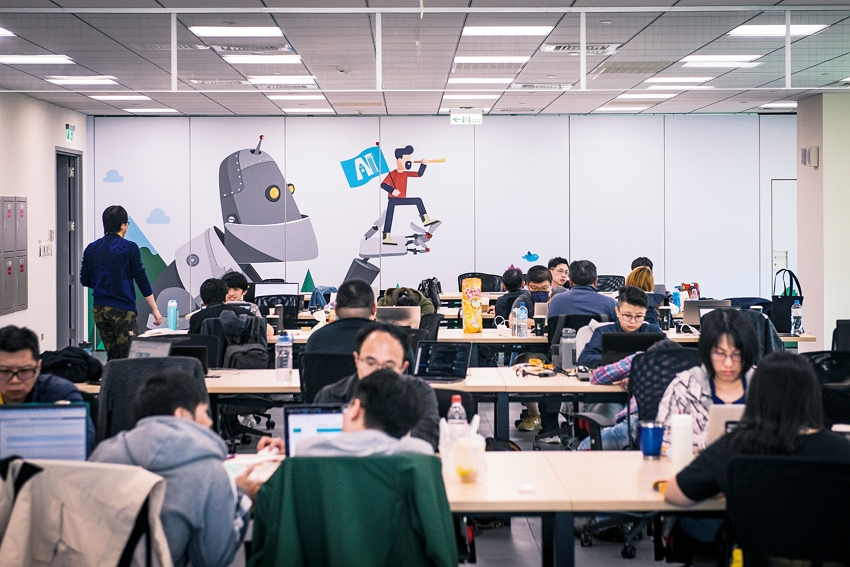
Taiwan AI Academy’s well-trained graduates will play an invaluable role in the business world. (photo by Kent Chuang)
It’s late fall in Hsinchu, and the November winds are bringing news of the harvest. At Fu Le Fishing Village, the fishponds stretch into the distance, but there’s not a person in sight and the only sound is the susurration of the wind. The local fish farmers are having a big day elsewhere, gathered at a nearby fish processing facility.
A large truck stands outside, the attached container filled with gray mullet netted early that morning. As the villagers crane their necks for a glimpse, the container opens and a veritable cascade of mullet spills out onto the floor. The harvest season kicks off to the sound of the fish and water pouring out of the container, and the simultaneous roar of the assembled villagers.
Xu Fengli, a member of the village’s production and marketing group, is the owner of the Chiafong fish farm. Xu left the Industrial Technology Research Institute 22 years ago to take over the business from his father. Now, still in the prime of life, he has become an important figure in the aging village.
Xu’s scientific approach to aquaculture reflects his background in science and technology and is quite different from the old-school approach of his father’s generation. His background is even apparent in his conversation, which never strays far from water quality indicators like dissolved oxygen levels, pH values, and oxidation-reduction potential (ORP).
Putting data to use
Some time later, we turn our faces to the wind and return to the fish farm. Fu Le Fishing Village is a pleasant, well-shaded place, and its fishponds are equipped with an array of monitoring equipment.
Xu recalls his early years in the business, feeling out the production process. He pored over texts, cramming his brain with the science he needed to develop his methods and negotiate the pitfalls in his path. He gathered water quality data with handheld sensors, tracked the changing numbers, and honed his approach. Then, two years ago, he purchased an automated smart aquaculture system developed by Quadlink Technology. It saves him a tremendous amount of work.
Xu relies heavily on Quadlink’s “Aquadlink Smart Aquaculture Application System,” which was developed in Taiwan. As with the “look, listen, smell, ask, feel” of traditional Chinese medicine, the system helps its users to diagnose and resolve problems.
The system consists of both monitoring and control components. The former are located in the fishponds, and test the temperature, pH, ORP, dissolved oxygen, and salinity of the water every five minutes, 24 hours a day. They upload this information to the cloud, where it is analyzed by artificial intelligence systems to anticipate future changes in water quality. If the AI foresees the potential for degradation, the system notifies the pond’s owner, who can then deploy the control system to take action remotely. For example, if the AI predicts a decline in dissolved oxygen levels, the pond owner can forestall the problem by turning on more aerators.
Otto Tsai, Quadlink’s president, explains that fish farming involves complex biological environments, and the “tricks of the trade” that traditional fish farmers like to hold close to their chests don’t hold up well to scientific scrutiny. Different fish, different environments and different production strategies all give rise to different requirements. That being so, anecdotal data from other farmers has limited utility.
“So instead we encourage aquaculturists to make their data open, because they can benefit from doing so. We help process their information, and can then tell them what they need to pay attention to. This saves them a lot of work and enables them to manage their ponds more effectively and reduce their risks.”
Aquaculture is a high-risk field. Moreover, farmers are aging without passing on their hard-won knowledge and experience. Artificial intelligence offers the prospect of turning around what might otherwise be a twilight industry, but farmers have to have access to AI to do so.
The Taiwan AI Academy
Do you want to build an AI? You first need talented people.
Something wonderful happened in November 2017, something that owes much to the vigor and flexibility of Taiwanese civil society. Recognizing Taiwan’s relative dearth of domestic AI professionals, a group of three academics: Academia Sinica president James C. Liao, academician H.T. Kung and research fellow Chen Sheng-wei, and two businesspeople: Waterland Financial Holdings chairman Wea Chi-lin and Top Taiwan Venture Capital chairman Andy T.C. Chiu, gathered to discuss the urgent need for the transformation of Taiwanese industry.
They could see the AI wave approaching, and realized it was essential that Taiwan ride it.
With this objective in mind, they approached Formosa Plastics, Chi Mei, Inventec, AU Optronics, Elan Microelectronics, and MediaTek, persuading each to invest NT$30 million to establish the Taiwan AI Academy.
This private-sector-driven initiative set the fires of change alight. The academy has drawn faculty from scholarly institutions ranging from Taiwan’s major universities to foreign research institutes, Academia Sinica and the Industrial Technology Research Institute, as well as from the corporate sphere, with AI managers and entrepreneurs coming in to share their real-world AI experience.
The academy offers students both management and technology courses. The former teach programming and other technical skills, while the latter help their students, largely senior executives with policymaking powers, develop a thorough overview of the AI terrain. While differently oriented, the courses of both types emphasize both theory and practical applications, challenge their students with exams and group projects, and quickly transform participants into AI pros with the skills businesses need.
The academy first opened in Taipei in 2018, but it has since expanded with branches in Hsinchu, Taichung, and Tainan. To date, its 200-plus teachers have provided more than 1.2 million hours of instruction to over 6000 students across Taiwan. Formosa Plastics and AU Optronics have been active participants, each enrolling more than 100 employees in the academy’s courses, and Quadlink Technology president Otto Tsai is himself a graduate.
Multidisciplinary cooperation
We next go to Machan International, located in Taichung’s Waipu District. On the day of our visit, Darren Chen, a special assistant at the company, and five Taiwan AI Academy alumni from other companies in various industries, have gathered together to follow up on a project they originally undertook as part of their management course at the academy’s Taichung branch.
“Come on. I’ll take you inside the factory for a look,” says Chen, after bringing them to Machan’s facility in neighboring Dajia District. Inside, different stations on active production lines stamp, bend, weld and paint metal sheets, which are finally packaged and loaded into containers to await shipping.
The group pauses at the painting area’s inspection station. Several inspectors are using flashlights to check the products for defects. Meanwhile, a camera mounted above the production line continuously films the finished goods.
When Chen began the management course a few months ago, he proposed a project based on his company’s production processes: “AI-based Defect Detection for Dynamic Coating Processes.” His hope was to develop an AI system that could use imaging to automatically detect defects, thereby replacing human quality assurance workers, who are fallible and have a high turnover rate. His presentation of the proposal piqued the interest of a group of classmates, and they formed a team to bring it to fruition.
Team members used their expertise in their own fields to contribute to the work. The proposed system’s use of image recognition requires first categorizing image data, and then using those images to train the machine to distinguish good products from defective ones. A classmate whose job involved quality control helped them establish the criteria for identifying defective products. Another classmate, a project manager, handled scheduling, expenses and manpower allocations. The academy then matched the group with someone in its technical program to do the necessary programming.
The team has long since completed the course, but for Machan their project was only the first step of its journey into the AI world. Chen explains that the four-month-long course provided them with only enough time to build the prototype, and says that they are still in the process of collecting image data. He anticipates that the system will achieve 95% accuracy within six months, at which point they will bring it online. Their next steps will be to connect the inspection system to the factory’s Internet of Things, and to match the system’s defect checking parameters to their manufacturing tolerances, so that they can begin to use the AI to carry out quality checks.
A fully developed version of the system should have applications at other firms that apply similar finishes to sheet metal, including those in the aerospace, machine tools, bicycle, and hand tools industries.
As important as AI is to Machan, it could be still more important to Taiwanese manufacturing as a whole. It has the potential to help traditional manufacturing businesses break free of the cost-cutting treadmill they have been stuck on. As Richie Tsai, chief operating officer of Taiwan AI Academy, says: “Taiwan has many hidden champions, but so what? We still can’t compete. In upgrading and transforming [our industries], we not only need to entice foreign firms to place orders here, we have to compel them to!” Can Taiwan become an AI powerhouse? Tsai is confident that we can.