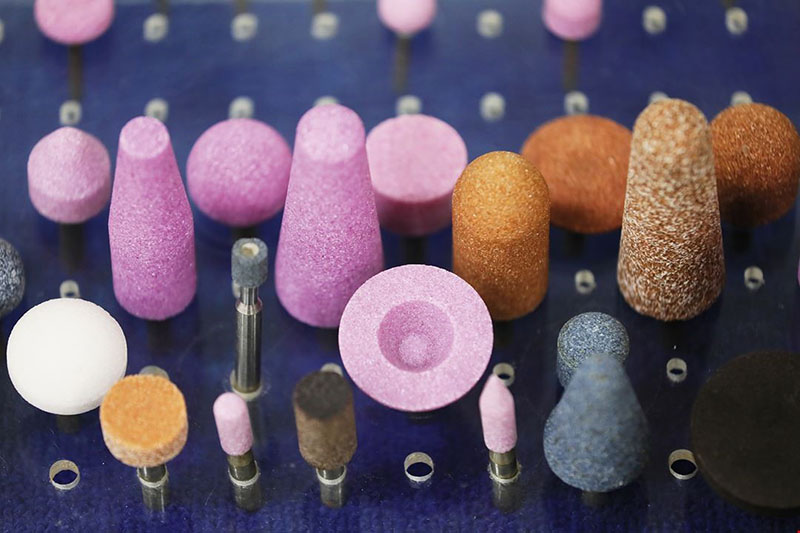
Abrasive mounted points of various types.
A grinding wheel—or “sand wheel” in Chinese—is neither a wheel made from sand nor a big-wheeled steamship that transports sand, but rather a tool that grinds or cuts a variety of materials such as plastic, wood, and steel. And Kinik Company (formerly China Grinding Wheel Corp.) is not a state-owned enterprise of Taiwan or of mainland China, but rather a privately owned company with a traditional manufacturing background, based in Yingge, New Taipei City.
Kinik, Taiwan’s “grinding king,” has continued to focus on its core strength of grinding. The company manufactures a range of 100,000 different grinding and cutting wheels, from huge ones 1.55 meters in diameter that grind ship crankshafts, to extremely thin ones only 0.03 millimeters thick, used to slice nano-wafers. In recent years Kinik has leveraged its expertise in high-speed grinding to move into products for the semiconductor industry, thus expanding into international markets. It ranks second by global market share in both diamond CMP pad conditioners and reclaimed wafers.
It is a dark and rainy day in northern Taiwan. The brick walls that greet one upon entering the Kinik factory in New Taipei City’s Yingge District impart a strong historical atmosphere, and the plant has indeed been designated a historic site by the Yingge District Office.
“Kinik has transformed itself every 20 years,” says CEO Thomas Hsieh. “From its focus on traditional grinding wheels as its core business, it has moved to highly efficient diamond wheels, and then to diamond CMP pad conditioners and reclaimed wafers.” Reclaimed wafers must be processed in cleanrooms, which the firm has built in its branch factories in Hsinchu’s Zhubei and Hukou and Miaoli’s Zhunan Science Park. These allow Kinik to be involved in semiconductor production while remaining a traditional manufacturer.
From tableware to reclaimed wafers
In its earliest incarnation Kinik was the Jin Ming Kiln Factory, which was once the leading producer of tableware in Yingge. But its owner Lin Chang-shou discovered that because the technical barriers to entry in ceramics production were so low, staff merely needed to work hard at mastering the techniques before they could leave to start their own factories. In 1953 Lin and his son-in-law Pai Yung-chuan switched to manufacturing grinding wheels, an industry that had higher barriers to entry. They changed the firm’s name to China Grinding Wheel in 1964. With Taiwan’s rapid shift from light to heavy industry, companies whose processes involved cutting and grinding needed abrasive wheels, and China Grinding Wheel could make all manner of customized products for its clients. Producing several thousand tons of cutting and grinding wheels per year, it was the top manufacturer of them in Taiwan.
When revenues stagnated, the company started looking for opportunities to transform. Kinik’s second-generation leader, Frank S. Lin, elevated the company’s products from traditional grinding wheels to high-precision diamond wheels. But he remained concerned about the company’s prospects, so in 1997 the firm commissioned the Industrial Technology Research Institute to develop a method to “reclaim” (refurbish) the silicon wafers used for process control tests in semiconductor production, on condition that the method make use of abrasive wheel technology.
Lin then dropped NT$100 million to build a new factory in Zhubei for a spin-off firm—Kinik Precision Grinding—led by Thomas Hsieh, who had been heading the company’s R&D team. It started to produce reclaimed wafers.
“I’ll always remember that in March of 2000 we got our first order for reclaimed wafers from TSMC—thus showing that our process could gain market acceptance,” says Hsieh. He continues, sotto voce: “Back then Kinik had annual revenues of only about NT$100 million. If we had failed, the company might have gone under.”
Fortunately, that “if” didn’t come to pass. Taiwan’s semiconductor manufacturers had previously had to send their wafers to Japan for refurbishing. Now able to get this done in Taiwan, they saved a lot on shipping. It was a win-win, benefitting both the semiconductor industry, for which time is money, and Kinik, which was very much looking to expand its range of products and expertise. As the fabs developed and produced eight- and 12-inch wafers, Kinik opened different lines of production and pushed different sizes of reclaimed wafers. Its consistent quality won favor with domestic firms such as United Microelectronics and Powerchip Semiconductor, as well as companies in the United States such as Intel and Micron Technology. Kinik rose to become a global leader in the field.
Sharpening makes the sword
In 1996 the company stepped into the field of “chemical-mechanical planarization” (CMP), whereby semiconductor wafers are flattened by polishing them with a rotating pad and an abrasive chemical slurry. During this process the pad must be continually “conditioned” to clean it of debris and replenish the slurry. Semiconductor manufacturers sought out Kinik to see whether their expertise in abrasive technology could improve the pad conditioning process. After lengthy research and experimentation, in 2000 Kinik began making pad conditioning disks with a uniform grid of evenly sized diamond particles instead of a randomly distributed grit as before. In 2002 TSMC recognized Kinik’s reliable quality control by giving it “ship-to-stock” certification, eliminating the need for quality inspections of its products on arrival at TSMC premises.
If you want to market niche products to the world, strong R&D is a must. Indeed, over the years Kinik has been granted 452 patents, 155 of which are currently in force. Hsieh explains rather matter-of-factly that the patents are part of the company’s external strategy. But internally the company has all manner of trade secrets involving formulas, production processes, and so forth. These represent an important way that Kinik stays a step ahead of the competition.
“The most important thing is that Kinik had a foundation in traditional grinding wheels,” observes Willie Pai, Kinik’s vice chairman. “From grinding wheels made with traditional abrasives, to diamond grinding wheels, to diamond CMP pad conditioners, we have firm foundations across the board.” Kinik views grinding as its core strength: Its grinding expertise is how the company has been able to vault itself from traditional manufacturing into the semiconductor industry.
Over 20 years, reclaimed wafers and pad conditioners have brought Kinik more than NT$40 billion in revenues—making it the leading firm in Taiwan and number two worldwide in both these fields.
Triumph from adversity
The guiding principle of abrasive machining is to grind using abrasives that are harder than the material being worked—for instance, Kinik makes alumina wheels for use on plastic and bakelite, while producing harder diamond wheels for tungsten steel, display panels, and optical glass. But when it comes to people, cofounder Pai Yung-chuang always took the approach that “soft works better than hard.”
Ever since he had to work as a janitor at Shalun Elementary School in Banqiao during the Japanese era because his family was poor, he was particularly grateful for the assistance of his father-in-law, Lin Chang-shou, who supported him to study in Japan. To repay his debt of gratitude, Pai contributed funds to build auditoriums at seven schools, including his alma mater Shalun, and to create the Lin Chang-shou Memorial Library in Yingge. He also set up the schemes whereby Kinik awards educational grants and scholarships to employees’ children, and issues gold coins to staff with more than ten years’ service, together totalling more than NT$100 million to date. The firm has also provided funding for high-level executives with backgrounds in fields such as mechanical engineering, geology and materials science to enroll in executive MBA programs. More than 20 of them have already earned their degrees.
Shaping the future
In step with industrial trends, the company’s output of reclaimed wafers and CMP pad conditioners has been increasing in recent years, whereas its output of abrasive wheels has been declining. That fact alarms Kinik, which had its start as a grinding wheel maker.
Three years ago Kinik acquired Yingge-based Hongia Industry and Thai-based Kinik-Thai. And the firm has expanded into the field of optics by producing molded glass lenses in a joint venture with Nihon Yamamura Glass, Japan’s biggest manufacturer of glass bottles. “We can’t survive just on grinding wheels, but we wouldn’t want to exist without grinding wheels,” proclaims Hsieh about the company’s core business as it looks towards a future of smart manufacturing based around its grinding expertise. Over more than 60 years of “grinding away” in its field, it has gone from grinding soybeans to grinding silicon wafers and has increased its revenues from NT$5 million to NT$5 billion. The company’s history demonstrates that so long as one’s skill is sufficient, it is possible—as the Chinese idiom goes—to grind needles from iron pestles.