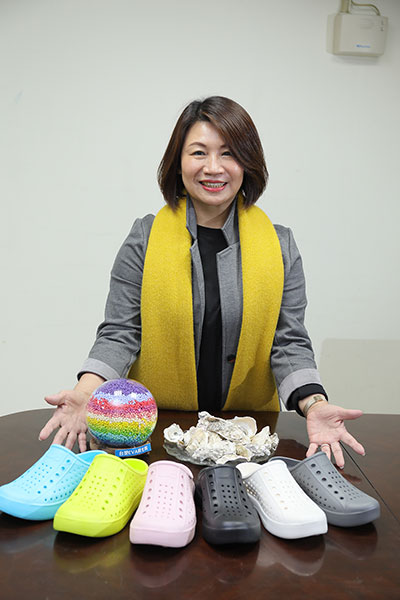
Through perseverance, Lu Shu-chen has created a homegrown Taiwanese sandals brand. The key to success has been her willingness to listen to what runners have to say and continually improve her footwear, making her sandals popular with Taiwan’s running community.
In 2021, Taiwan ultramarathon runner Lo Wei-ming finished second in the world’s longest certified road race, the Sri Chinmoy Self-Transcendence 3100 Mile Race, setting a new record for Asian runners. Athletes from around the world were not only in awe of Lo’s focus, they were also greatly interested in the “Y Sandals” (thong sandals) that he was wearing on his feet. The idea that someone would run a marathon in sandals became an international topic of conversation. Meanwhile, Taichung-based AP Plasma Corporation is using artificial intelligence and its “Air Aurora” bonding technology to “make shoes with air.” This integrated technology is being exported overseas, helping the shoe industry to escape its reputation as a polluting industry and produce shoes in an environmentally sustainable way.
In September of 2021, Lo Wei-ming took on the challenge of the Sri Chinmoy Self-Transcendence 3100 Mile Race, also known as the “Mt. Everest Ultra Run,” and finished second, showing exceptional willpower. He became the first competitor from Asia to complete the event in its 25-year history.
A classic ultramarathon
The Sri Chinmoy is the world’s longest certified road race at 3100 miles or nearly 5000 kilometers, roughly the distance from New York to Los Angeles. Participants must complete the race, which is held in the New York borough of Queens, in 52 days. They must make more than 100 circuits per day of the half-mile course on city streets, running it 5649 times in total during the contest. It is an extreme test of the competitors’ physical conditioning, endurance, and willpower. As of 2020 less than 50 people had completed the competition.
While running this race Lo wore a pair of Y-thong sandals, which left competitors from around the world dumbfounded. By the second half of the contest these runners had blisters on their feet, and seeing Lo continuing to run easily in his sandals, they followed his example and put on sandals themselves. This made an interesting side story for the race, and brought widespread international recognition for Made-in-Taiwan racing sandals.
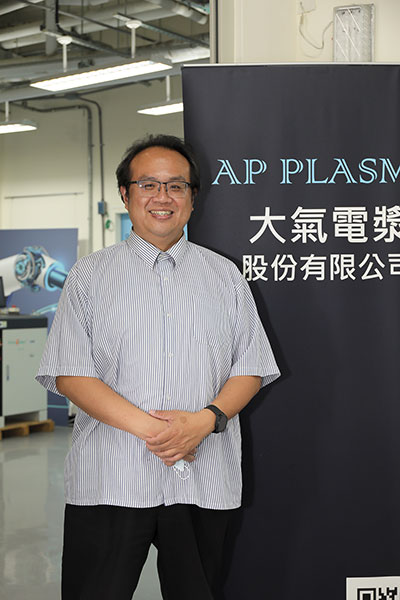
AP Plasma founder Jango Chang is quick-thinking and very knowledgeable, and has won an R&D 100 Award (from the US-based R&D World magazine) and a Wall Street Journal Technology Innovation Award.
Beloved of long-distance runners
Many of Taiwan’s ultramarathoners wear Y-thong road racing sandals when competing. Huang Po-hsiung, general secretary of the Taiwan Technical Textiles Association (TTTA), and Dr. Lee Jiun-chang, Taiwan record holder for the 48-hour Taipei Ultra-Marathon, are both fans of thong racing sandals. What magical attraction do Made-in-Taiwan racing sandals hold for these long-distance runners? For the answer we must look to the behind-the-scenes heroes at the Decheng Footwear Group, and the amazing antibacterial oyster shell powder developed by the Formosa Plastics Group.
Taiwan produces some 160,000 metric tons of waste oyster shells per year, leading to environmental pollution when they are dumped in coastal areas. In keeping with the ideal of the circular economy, Formosa Plastics processes waste oyster shells by calcination followed by grinding them into powder using special equipment to micronize the grains. This oyster shell powder is mainly composed of alkaline calcium carbonate, and generates reactive oxygen species that can break down the cell membranes of bacteria, making it an effective antibacterial material.
Last year, while watching the Taipei Ultra-Marathon, Formosa Plastics Corporation chairman and president Jason Lin noticed that Lee Jiun-chang was wearing B&M Caiman brand “Y Sandals.” Realizing that running marathons in sandals was a trend, he instructed his company’s R&D team to investigate the possibility of incorporating antibacterial oyster shell powder into ethylene–vinyl acetate (EVA). With this in mind they sought out Decheng Footwear, one of their long-term partners.
The secret to making thong sandals
Decheng’s OEM factory, located in Taichung’s Fengyuan District, is bustling. Workers busily place what look like mini-sized baby shoes into a machine, and after six to 12 minutes the shoes puff up into adult-sized air-cushioned footwear—it’s an amazing sight. Decheng general manager Lu Shu-chen says with a smile that this manufacturing process is “like making popcorn.”
When Formosa Plastics sought out Decheng in 2020 in hopes of developing sandals with antibacterial oyster shell powder, the project proved to be a huge headache for Lu. “At first we assumed that making the sandals would be like making boba tea: All we had to do was add the powder and stir, and everything would be fine. But in fact adding the oyster shell powder changed the physical properties of the original formula.” The result was that all of the “popcorn” produced by the machines had to be discarded. Formosa Plastics then began to adjust the properties of the oyster shell powder, in a process of trial and error that extended the product development period to two years.
When ultramarathoner Lo Wei-ming wore Made-in-Taiwan “oyster-tech” thong sandals in New York, he was realizing a long-held dream: “I wanted to raise Taiwan’s visibility, to bring a Taiwanese product to international attention.” His success was the ultimate testimony to the technological breakthroughs of Taiwan’s footwear industry.
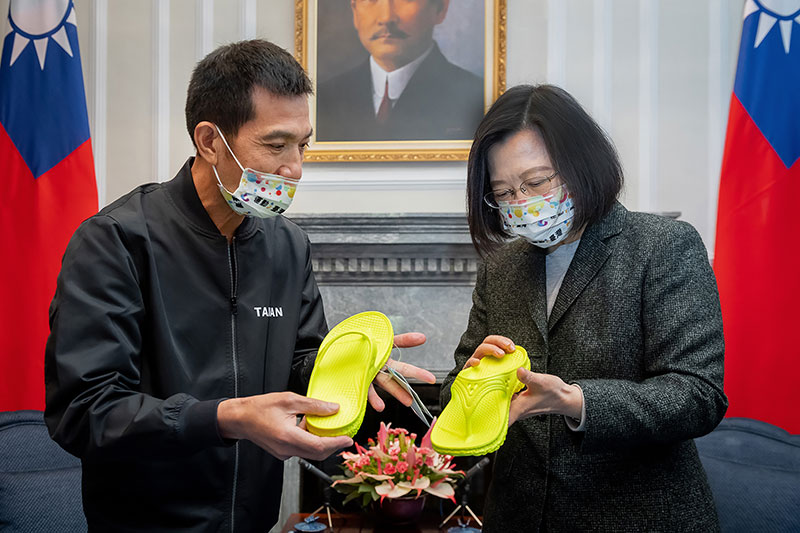
Ultramarathoner Lo Wei-ming successfully ran the world’s longest certified road race in New York in 2021. He became the first guest received by President Tsai Ing-wen on New Year’s Day 2022. (courtesy of the Office of the President)
A revolution in shoes made with air
Another Taichung-based firm with outstanding shoe manufacturing technology is AP Plasma Corporation, a start-up that prides itself on “making shoes with air.” In the display area of the AI Robotics Hub at the Central Taiwan Science Park, company founder Jango Chang points to a machine and says, “Come and feel it for yourselves.” Installed inside the machine is an “Aurora Jet,” which is a plasma gun shaped like the tail of a rocket, named for the aurora or polar lights visible in the Earth’s atmosphere due to ionization of particles caused by the interaction of the solar wind with the Earth’s magnetic field. When the device is turned on it immediately emits a ring of what appears to be flame, through which Chang moves his hand without fear of injury.
“The ‘flame’ produced by this device is an artificial aurora, and using this technology we can bond different materials together without traditional adhesives.” Chang, who sports an Einstein-like shock of curly hair, has developed the “3D Air Aurora” system (ATM-3), controlled by artificial intelligence, which uses a plasma jet generated by the ionization of air to prepare shoe sole elements for bonding, replacing the mechanical buffing and toxic organic adhesives used in the traditional manufacturing process. This innovative invention can reduce the average time for buffing and bonding each pair of shoes from one minute to ten seconds, and eliminates the need for toxic chemical primers and adhesives. For this it won an Energy Globe National Award in 2020.
AP Plasma vice-president Raymond Lin leads us to an ATM-3 machine, where we see the machine’s robotic arm moving rapidly as is directs the plasma onto the shoe sole components on the conveyor belt. The shoe soles come in different shapes and colors, and the plasma jet takes only a few seconds to complete its task, moving across the entire surface of each workpiece at astonishing speed.
Lin explains the principle behind the process. Traditionally in footwear manufacturing, shoe sole components are buffed with abrasive wheels, treated with chemical agents, pickled with acid, washed with alkali and coated with primer before adhesive is applied to bond the layers together. AP Plasma’s Air Aurora technology replaces these complex preparatory processes, reducing them to a few seconds’ work, and allows the soles to then be bonded with a water-based cement. The procedure produces no pollution, and uses only air as a raw material; it really shows the power of intelligent manufacturing.
AI development and the future
The traditional shoe industry features high-volume production based on numerous diverse, low-volume orders, and is labor-intensive and highly polluting. AP Plasma’s ATM-3 directly resolves a major source of pollution in the manufacturing process, helping firms move toward their environmental, social, and governance (ESG) goals. Besides the Air Aurora system, other factors that give AP Plasma a competitive advantage within the industry include the use of image recognition (using AI algorithms and deep learning technology) to determine the path of the plasma jet, and the company’s integration of the manufacturing experience of local shoe factories.
This technology has already been exported to Southeast Asia and incorporated into the manufacturing processes of brand-name footwear makers. Jango Chang, looking at future trends, feels that with the continuous development of AI technology, there will be a great deal of surplus manpower and industries will have to transform themselves. But the technology included in the ATM-3 can perhaps be transferred to many small and medium-sized enterprises, and even into ordinary homes. “Perhaps in the future there will be a robotic arm in the corner of every living room, turning them into ‘homes that are also factories’”—an updated version of the 1970s drive to promote industrial outworking.
To achieve global environmental sustainability, Taiwan’s footwear industry is continually working to upgrade technologically and find ways for mankind to live in harmony with the environment. Let us hope that improvements in shoe manufacturing technology can help preserve a beautiful homeland for our children.
For more pictures, please click《Putting Their Best Foot Forward: Taiwan’s Shoemakers Break New Ground》
Link《President Tsai reaffirms commitment to sports development in Taiwan》