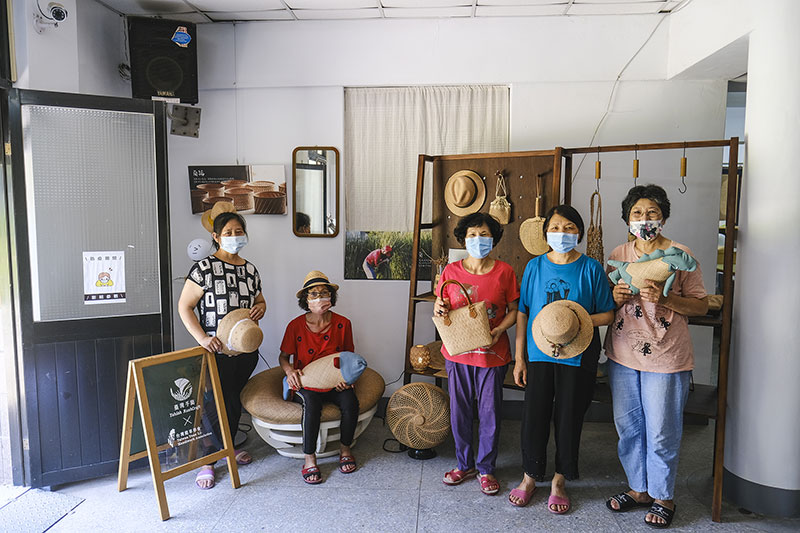
The Taiwan Yuan-Li Handiwork Association brought former rush weavers back to the craft to create household products that heal mind and body and suffuse life with the fragrant scent of rush.
TAs far back as the Qing Dynasty, gentry visiting Taiwan would return home with sleeping mats woven from triangular club-rush. Even then they made great souvenirs and gifts. During the Japanese era, rush products comprised the third largest category of exported agricultural goods, and the rush weaving industry brought prosperity to the town of Yuanli. It wasn’t until the 1970s that the industry there gradually began to fade away. Yet in the past 20 years, thanks to the efforts of many, artisans have come back to the craft, both reviving traditional rush weaving and giving it a modern twist.
On a sunny summer morning we walk into a space behind Cihu Temple in Shanjiao Village of Miaoli County’s Yuanli Township. The natural fragrance of triangular club-rush fills our noses. Artisans with strong hands, their fingers bound with protective tape, bend over their work as they focus on pulling and shaping rush strands. Day after day, they weave and finish rush handicrafts here.
Here at the Taiwan Yuan-Li Handiwork Association, many of the artisans have 50 or 60 years of experience weaving. Almost all Yuanli women of a certain age can remember weaving rush in tandem with their mothers.
Woven prosperity
The art of rush weaving has been passed down in the area for nearly 300 years. Way back in the 1700s, lowland indigenous people wove mats out of the wild rush that grew along the lower stretches of the Da’an River. Later the craft would come to nearby Han Chinese settlements such as Yuanli and Dajia. Gradually, artisans developed more elaborate techniques, such as weaving three-dimensional shapes.
With more and more people weaving rush, an industry gradually took shape. There were many roles to fill: rush farmers, weavers, middlemen who brought product samples for weavers to copy and collected the woven products, and the hat and mat dealers. Because the planting environment for rush is similar to that of paddy rice, families with wet fields would plant rush in a portion of them. The men would handle the farming, and the women and children the weaving. Dealers who collected finished goods from these communities grew familiar with the weaving styles and strengths of different producers. Serving as conveyors of information, they would bring samples to the weavers they thought were best able to produce them.
The dealers would pay for the goods in cash and could even provide weavers with advances. That money provided a financial cushion in hard times. Countless Yuanli women used their earnings from weaving to support their families, meeting living expenses and paying their children’s school fees. Girls, meanwhile, learned the craft at their mother’s side, as rush weaving became an integral part of Yuanli’s socioeconomic DNA.
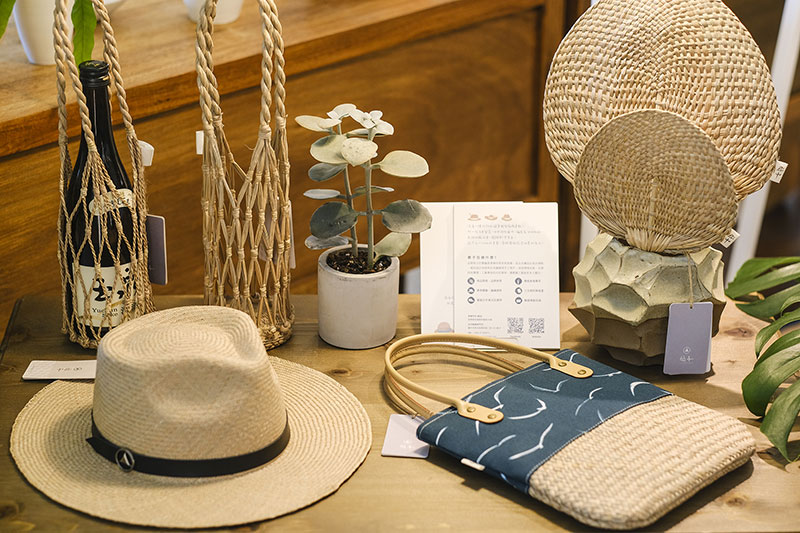
No two handmade rushwork products are exactly alike.
Preserving a Taiwanese craft
Though grass weaving techniques are found around the world, Taiwan’s rushwork is quite unique. It makes use of Schoenoplectus triqueter grown in the area north of the Da’an and south of the Yuanli rivers. It is called “mat grass” in Taiwanese and “triangular club-rush” in English (though botanically it is neither a rush nor a grass, but a sedge). The area’s unique soil and its location in the zone where the island’s northern and southern climates meet have led to special characteristics of the plant here. Research by the Japanese-era botanist Yaichi Shimada showed that the rush was tough yet supple and had excellent hygroscopicity and a fragrant aroma. Some tried to cultivate the plant in China’s Fujian and Guangdong. Although it would grow there, it lacked the excellent attributes of the triangular club-rush grown in Yuanli.
Taiwanese club-rush’s toughness, resistance to sun damage, breathability, unique scent, and beautiful coloration (with varying shades of green, yellow and brown after exposure to the sun), as well as the exquisite techniques of weavers here, made the island’s rushwork products widely treasured. The colonial government even established an industrial association to manage the export of rush hats.
Yet as Taiwan actively promoted industrial development in the 1970s, the rush weaving industry went into decline, and most of this small town’s hat and mat makers closed one after another.
Though the boom times were over, surviving firms like Zhen Fa Hat and Mat, Jiancheng, and Meitian continued to pass down Yuanli’s weaving culture. Meitian’s owner Luo Lifen, a Yuanli native, recalls those days when the market seemingly shrank overnight and many weavers left the industry. Even if you were approached with a large foreign order, you wouldn’t dare accept it.
In 2002 the Yuanli Farmers’ Association made plans to establish an exhibition hall to display the area’s historical rushwork products, and they asked Luo to work with them. She helped them to find rush material and went throughout the township to recruit seniors to start weaving again. Smiling, she says that the old weavers still held a deep affection for the craft and were very willing to come back to it when given the opportunity. Once the tools were in their hands, memories of the weaving techniques returned.
Skills rediscovered
In addition to the perseverance demonstrated by the rush hat and mat industry through hard times, the Taiwan Yuan-Li Handiwork Association also played an important role in reviving the craft. The techniques of rush weaving take a long time to acquire, and processing the rush ahead of weaving is an even tougher test of these artisans’ skills. It requires taking a needle to split the rush into two or three strips, before splitting those into even finer strips. These thin strands of rush make the weaving process more labor intensive, but the resulting products are finer.
Yeh Wen-hui, founding chairman of the association, couldn’t bear to see the craft die out, and in 2003 he started to promote weaving in Yuanli’s Shanjiao community, which is where the farmers’ association would later build its Rush Exhibition Hall. The sight of the artisans gathering together to weave and exchange techniques recalled images of the industry’s heyday years before.
Yeh formally established the association in 2009. Apart from the rush-weaving classes it offers at Shanjiao Elementary School, he has also worked with Professor Lu Chia-hui of the Tainan National University of the Arts to publish the books Chronicle of a Rush Weaver and Rush Weaving: Daily Lessons. Furthermore, with the weaving courses offered at the university, Lu has turned rush weaving into a medium of youthful creativity. Huang Zeng-jhen, secretary-general of the association, believes the seeds spread by these weaving memories will surely bear fruit.
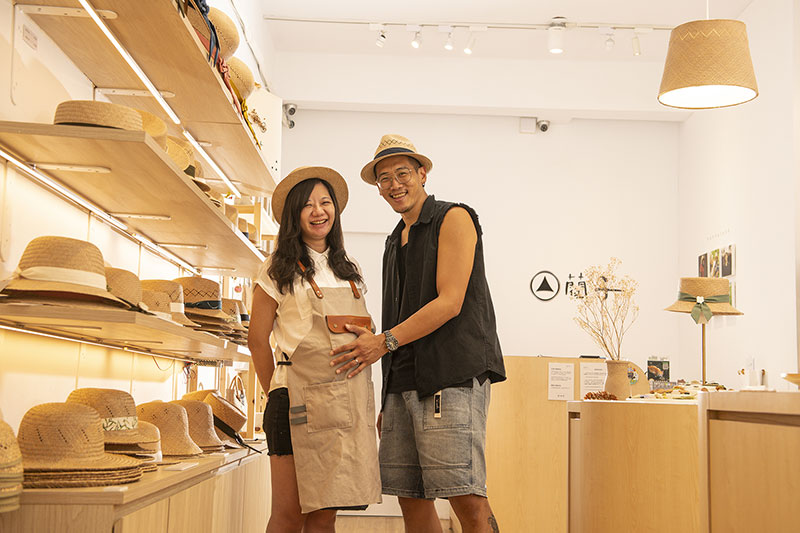
By founding Sunnyrush, Lila Liao (left) and Eason Lee have breathed new life into the rush weaving industry with their fashion-forward designs.
New rushwork businesses
In 2015 designer Chen Shao-yen, then based in London, wanted to create some dresses based on traditional Taiwanese weavings, and eventually found his way to the association. Although they had never made rushwork clothes before, two weavers, Liu Caiyun and Wu Caiqing, rose to the challenge, working for a full month to finish the order. When the actress Shu Qi wore a beautiful corset-like vest to a charity benefit, it both surprised the public and demonstrated the boundless potential of rush weaving.
The rich cultural heritage of the craft has attracted young people, who have given it a fashionable contemporary twist and used it to bring beauty into people’s daily lives. Take, for instance, the designer brand Sunnyrush. Its founder Lila Liao originally studied industrial design, which has an emphasis on mass production. By chance, she came across the Handiwork Association and fell in love with the uniqueness of its woven products, working there in several capacities during college and after graduating.
In 2016 she and a fellow worker at the association, Eason Lee, founded Sunnyrush to explore how young people could make a living with rush weaving. At first, weavers wondered how serious they were and were reluctant to commit too much to them. But Liao and Lee spent a lot of time with the weavers, getting to know their personalities and the strengths of their techniques. Lee would go as far as to drive a weaver home to her son’s house or to transport deliveries of rush material when it was on his way. Recognizing their sincerity, the weavers came to see that the two truly wanted to make their way in the industry. One by one, weavers joined the Sunnyrush team, which came to number as many as 41 last year.
Making rush all the rage
At the Sunnyrush store in Yuanli, the bright space and the refined sense of design apparent in its sales displays impart a whole new view of the industry. Samples of traditional weaves—such as “net,” “feather” and “pineapple”—are hung on the walls. These weaves are used in Sunnyrush’s fashionable hat designs. Apart from the fedora-like “jazz hat,” which was exported in large quantities during the Japanese era, Sunnyrush drew inspiration from the hats worn by Venice’s gondoliers for a boater. They have matched these woven hat types with their own printed fabric designs that capture the essence of Yuanli, or with hat ornaments or bands handmade for them by various Taiwanese craft brands, using materials such as embroidery, wood or woolen felt. These add richness to people’s image of woven rush hats.
Firmly believing in the quality and value of woven rush, within a year of its opening Sunnyrush began selling a rushwork bag reinforced with vegan leather. Despite selling for more than NT$7,000, the bag has been a hit with customers, demonstrating that traditional Taiwanese woven bags can meet the highest of standards.
Before the pandemic, Sunnyrush was already selling its woven rush products in a Japanese craft store and had created some products together with the Japanese brand Sou Sou. Meitian’s Lou Lifen is preparing to export rush insoles for Japanese wooden clogs. And the Taiwan Yuan-Li Handiwork Association, under the auspices of the Ministry of Culture, has traveled abroad repeatedly—to a craft fair in Berlin, to London Craft Week, and to Chiang Mai Design Week, among others. Featured in international exchanges, these rushwork products have impressed foreign consumers. Thanks to the efforts of so many to protect this craft and pass down its heritage, these fragrant strips of sun-dried rush, employed in all manner of beautiful ways, are drawing attention far and wide.
For more pictures, please click《Yuanli’s Rush Weaving Renaissance》