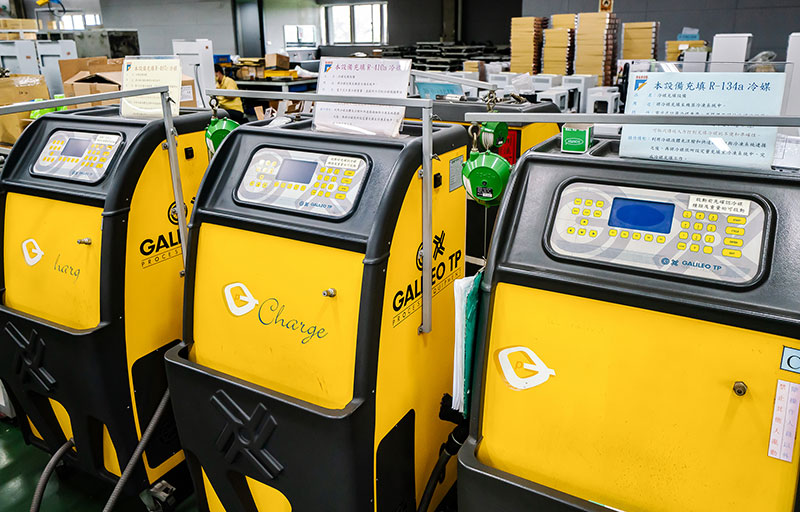
Faced with waves of change such as the trend toward intelligent manufacturing and the drive for net zero carbon emissions, Taiwan, the world’s fifth largest exporter of machine tools, has organized a carbon neutrality alliance and is actively pursuing carbon reduction by developing energy-saving technology for the spindle drives of advanced machine tools, as well as smart energy-saving products.
As you head off to work in the morning, you pop into a convenience store and pick up a coffee and some breakfast. This is a daily routine for many people. But have you ever wondered where such a convenient lifestyle originates?
Omnipresent machine tools
Almost everything around us in daily life, from airplanes to air conditioning to packaged food, is produced by machines. And for all machinery, including textile machines, plastic injection molding machines, and automated equipment used in semiconductor manufacturing, the components they are built from are made by machine tools. “That’s why we call machine tools ‘the mothers of machines,’ because they are machines that make machines,” says Christopher Mai, a division head at the Intelligent Machinery Technology Center of the Industrial Technology Research Institute (ITRI).
Mai says that the machinery industry is an old and venerable one, and that the global industrial revolution started from the machinery industry. “Furthermore, the development of precision machinery is an indicator of a country’s industrial level.” Machinery is the wellspring of production and manufacturing. For example, if you want to develop solar power you must have machinery that can cut solar panels. In terms of semiconductors, without the right machinery firms like the Taiwan Semiconductor Manufacturing Company could not carry out advanced manufacturing processes. Therefore the development of machine tools is an important foundation for all industry.
In Taiwan, more than 90% of companies in the machine tool industry are small and medium-sized enterprises (SMEs). They have outstanding flexibility and R&D capabilities, assuring them a place in the international market. For example, the Fair Friend Group, the world’s third largest machine tool conglomerate, includes Boeing and BMW among its customers, making the Taiwan-based group a genuine “hidden champion.”
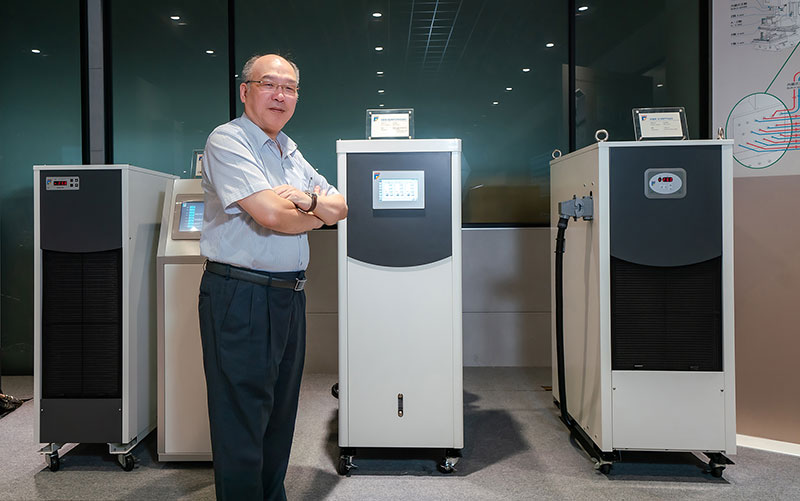
Habor Hsu, who well understands the urgency of achieving net zero carbon emissions, has led Habor Precision toward smart energy-saving technology, enabling Taiwan to hold its own in the global market for cooling systems.
Technology R&D for the future
For a modern machine tool to function, besides the machine itself another critical core part is needed: a controller—the “brains” of a machine tool, which controls its operations through instructions from software programs. In the past, the global market for controllers was dominated by Japan and Germany.
Only with autonomy in the area of controllers can one increase the value-added of machine tools. This is why ITRI invested so much effort into R&D for domestically produced advanced computer numerical control (CNC) units and successfully transferred this technology to businesses, in hopes that they can develop machine tools that are more closely customizable to clients’ needs.
Over the past several years Taiwan’s machine tool industry has been engaging with the trend toward intelligent manufacturing, and has gradually found its feet. This was soon followed by the issue of climate change and the drive for net zero carbon emissions. Habor Hsu, chairman of the Taiwan Machine Tool and Accessory Builders’ Association (TMBA) and president of Habor Precision Inc., an internationally prominent maker of cooling systems, stresses that firms need to approach both topics one step at a time.
Hsu notes that each machine tool includes countless parts, and the industry must collaborate with government and academia to analyze the carbon emissions at each stage of their manufacture and of the machine tool’s operation. Then the association must provide this information to firms so that they can consider how to make further progress towards optimization. Meanwhile in June 2022 ITRI signed an agreement with Feng Chia University to form the Alliance for Carbon Neutrality, to assist machine tool makers to conduct inventories of greenhouse gas emissions and then, with the help of big data analysis, implement smart job scheduling and resource allocation so that machine tools can be operated in a more energy-saving way.
The carbon reduction technology developed by ITRI for advanced machine tool spindle drives can reduce energy use by 70% compared to traditional drives. It conforms to the EU’s standard for high energy efficiency, under category IE2. With the EU launching trial implementation of its carbon tax next year, this technology offers a solution for energy saving and carbon reduction.
Carbon impact
However, it is not only in the last two years that the EU has launched policies to combat climate change. Habor Precision felt the impact of new rules as early as 2017.
“During the Lunar New Year holiday we got a call from overseas saying that our coolers couldn’t clear customs because we hadn’t paid our taxes,” recalls Sylvia Hsu, special assistant to Habor’s CEO. Baffled, she hurriedly contacted international sales manager Fran Wu. Only then did it emerge that the problem was the European Union’s F-Gas Regulation, which requires equipment containing fluorinated greenhouse gases to be registered and a tax to be paid. Such gases are widely used as refrigerants in cooling systems.
Habor Hsu says that after Habor Precision had been active in the European and Japanese machine tool markets for many years, in 2015 two international clients in succession raised the need for products that could achieve carbon reduction. “Thus we realized fairly early on that carbon reduction and energy saving would be the trends of the future.” Habor consequently replaced energy-intensive cooling and lighting equipment in its own factories, began promoting paperless operations, and planted many trees on its factory grounds. Even in the sweltering heat of summer, the natural cooling effect of this vegetation provides a noticeable reduction in temperature.
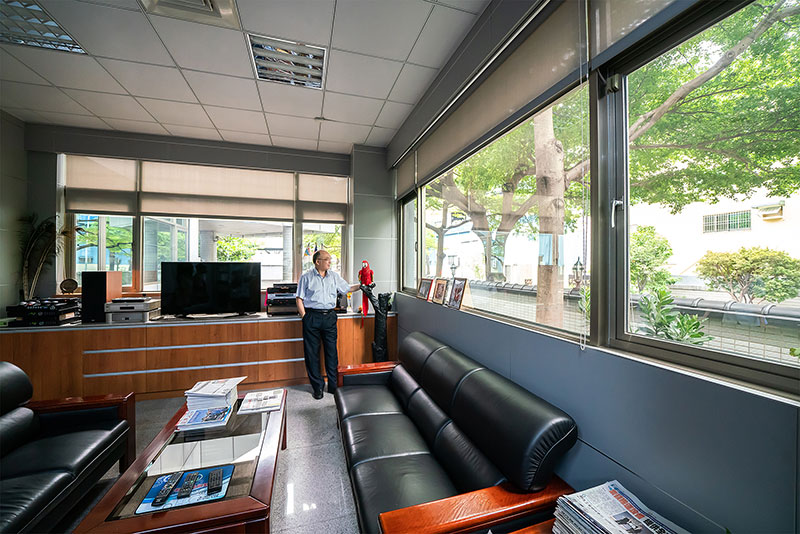
As chairman of the Taiwan Machine Tool and Accessory Builders’ Association, Habor Hsu sees energy saving and carbon reduction as the future direction of business operations. He proactively shares his views with his industry colleagues in hopes that the machine tool industry can advance toward net zero carbon emissions.
Alliances for international impact
The more demand there is for high-precision, high-efficiency manufacturing equipment, the greater the need for cooling systems to control the temperature. This applies in particular to industries such as semiconductors, aerospace, and information and communications technology.
Given the urgency of combating climate change and international demand for low-carbon-emitting and low-refrigerant products, Habor developed cooling systems that use ozone-friendly refrigerants, reduced quantities of refrigerants, or no organic refrigerants at all. They have set up an environmental laboratory to ensure that products can cope with the different environmental conditions in various countries, as well as differences in the available electrical supply. They have also introduced designs utilizing the Internet of Things and smart device management. For example, the design of the intelligent DC inverter cooler for which Habor won a Taiwan Excellence Award in 2022 incorporates both an inverter control and an energy-saving system, and its operation can be monitored and controlled remotely by software to help customers achieve the goal of smart and effective management.
Habor Hsu states that to create products that will satisfy future demands, it is not enough for his company to rely on its own efforts alone. The supply chain, such as makers of compressors and refrigerants, must also cooperate in their development. Every component must be intelligent and energy-saving, and only with everyone working together to upgrade product performance can positive results be achieved.
Taiwan boasts outstanding capabilities in information and communications technology (ICT) and a comprehensive industrial chain in precision machinery. In recent years, many alliances have been launched within Taiwan’s machine tool industry. These have included a group to promote “software as a service” cloud services for intelligent manufacturing, a cross-industry group to promote localization of semiconductor equipment, and so on. They are bringing together the machine tool, ICT, aerospace, and semiconductor industries as well as research institutions, and integrating the resources of industry, government, and academia to drive industrial transformation. In the face of trends toward intelligent manufacturing and net zero carbon emissions, all these stakeholders will work together to build up the reputation of Taiwan’s machine tool industry in the international market.
For more pictures, please click《Energy Saving and Net Zero—The Future of Taiwan’s Machine Tool Industry》