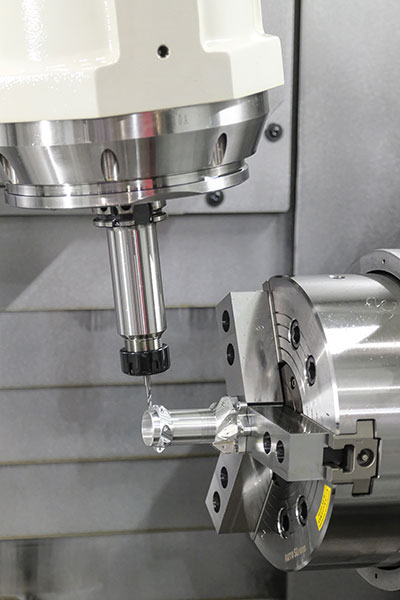
This five-axis multitasking machine produced by Goodway Machine Corporation can form workpieces into various complex shapes. This capability enables Taiwan’s machine tool manufacturers to penetrate the market for the aerospace and electric vehicle industries.
The 2023 Taipei International Machine Tool Show (TIMTOS), the first show of its kind in the world this year, was held in March. Taiwanese exhibitors presented solutions involving automation, intelligent machinery, and zero carbon emissions, exemplifying the trend toward optimization and innovation in machine tools.
Currently Taiwan ranks second in the world in exports of shoemaking machinery, fifth in exports of machine tools and of plastics and rubber machinery, and sixth in exports of textile machinery and semiconductor equipment. As a country renowned for its manufacturing of precision machinery, “Taiwan not only makes export products with a high performance to cost ratio and provides excellent 24-hour on call service, we can also work with clients to solve existing and future problems and bring next-generation products into existence,” says Tommy Hsu, president of the Taiwan Association of Machinery Industry, as he points out the highlights of TIMTOS 2023.
TIMTOS, which in 2019 became the world’s third largest machine tool exhibition, was held in Taipei in March of 2023. The 6,200 booths attracted more than 6,000 overseas buyers, approaching pre-pandemic levels, and more than US$2 billion worth of orders were placed.
Taiwan-based Fair Friend Group, the world’s third-largest manufacturer of machine tools, demonstrated rotary transfer machines that can be expanded to have more than 12 workstations, and emphasized that three such machines can operated by one machinist. One of the machines on display can turn out parts for electric vehicles at a rate of one every 8.8 seconds, and has been dubbed a “license to print money” by people in the industry.
TTGroup, focusing on technological transformation in the areas of both digitization and carbon reduction, showcased “digital twin” simulation technology that can achieve true integration of virtual and physical resources covering everything from discrete machining operations to individual machines to entire production lines, thus demonstrating the potential of integrating machinery, electronics, and software.
Meanwhile, Quaser Machine Tools displayed a carbon emissions calculating system for machining operations, which will become standard equipment on machine tools. The system uses various operating parameters gathered during machining to calculate the volume of carbon emissions. It caters to potential future demand from customers for calculating the carbon emissions of each part produced, which can help them learn the carbon footprint of their products and pursue low-carbon production.
Jywe Wen-yuh, a distinguished professor in the Department of Mechanical Engineering at National Taiwan University, opines that these remarkable product designs are evidence that Taiwan’s machine tool sector has the ability to thoroughly remold itself and provide value-added services including smart manufacturing, digital transformation, and low-carbon sustainability.
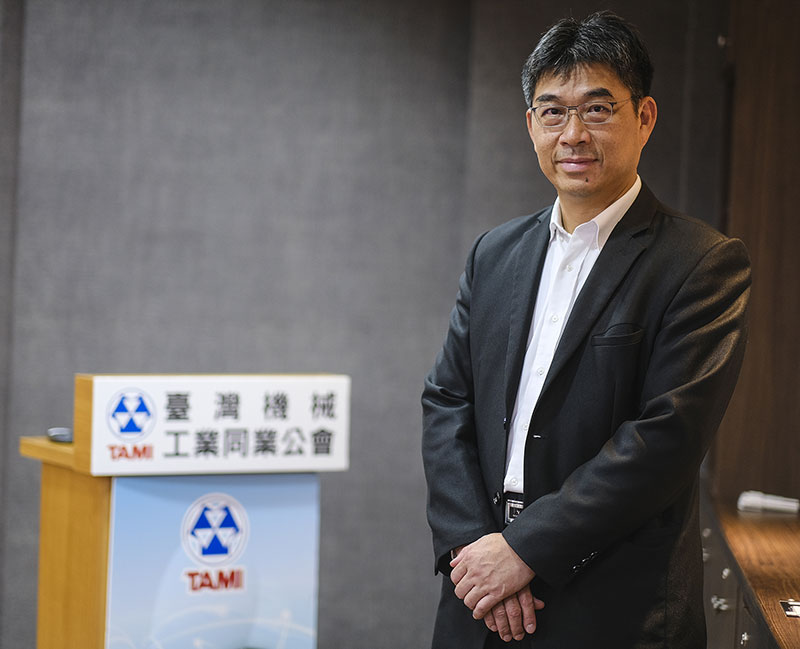
Tommy Hsu, president of the Taiwan Association of Machinery Industry, says that Taiwan is developing smart machinery in order to provide solutions that meet customers’ needs.
Smart manufacturing: Taiwan’s opportunity
According to data from the Taiwan Association of Machinery Industry (TAMI), the output value of Taiwan’s machinery industry reached NT$1.1 trillion in 2017, making it the third industry in Taiwan to exceed NT$1 trillion, after semiconductors and display devices. The sector’s output value and exports have risen steadily, reaching new heights in 2022 with an output value of NT$1.45 trillion and exports worth US$34.8 billion. The latter figure is 2.26 times higher than the US$15.4 billion in exports it achieved in 2007.
TAMI president Tommy Hsu says that a critical factor in this growth has been coordination between TAMI and the government to promote the development of the smart machinery industry since 2016.
Take for example the five-axis multi-tasking machine produced by Goodway Machine Corporation, which won the Grand Champion Award in the computer numerical control (CNC) lathe category at the Taiwan Machine Tool Industry Awards for Excellence in Research and Innovation, presented at TIMTOS. The machine integrates multiple manufacturing processes including turning, milling, and gear hobbing. It has powerful cutting capabilities and is able to make parts with complex shapes. At TIMTOS, Goodway posted notices of orders received from the Aerospace Industrial Development Corporation and from TURVO, indicating that this five-axis machine can produce complex parts for the aerospace and electric vehicle markets.
TTGroup, which describes itself as a “total solutions provider,” exhibited an autonomous mobile robot that can load and unload workpieces, a system that can perform prior simulation of complex machining operations to identify difficulties that might be encountered, and automated solutions to improve machining quality and reduce swarf accumulation at the tool tip.
Industry 4.0
Tommy Hsu, who previously served as a division director at the Mechanical and Mechatronics Systems Research Laboratories of the Industrial Technology Research Institute, emphasizes that Taiwan’s machine tool sector no longer merely sells products, but “total solutions.”
Jywe Wen-yuh, who is very familiar with the global machine tool industry, has noticed that Taiwanese machinery manufacturers have promoted innovation by founding new companies. They have carved out a share of the niche market for systems integration by responding to the needs of end users. For example, YCM, a venerable machine tool maker that has been around for nearly 70 years, founded Dot Zero, while Syntec Technology, one of Taiwan’s major producers of CNC controllers, established Leantec. New firms like these are working to satisfy the manufacturing sector’s demand for various types of transformation.
Parts for the aerospace and electric vehicle (EV) industries require high degrees of quality and reliability. Tommy Hsu states that thanks to the impetus provided by the “Mobility In Harmony Alliance” and its open EV ecosystem platform created by the Aerospace Industrial Development Corporation and the EV division of the Hon Hai Technology Group (Foxconn), major Taiwanese machine tool firms, taking a “Team Taiwan” approach, been able to join in the supply chains for the aerospace and EV industries.
In recent years, Taiwan’s machine tool manufacturers have exhibited at overseas trade fairs in national pavilions based on the concept of a “Taiwan cluster.” In this way they have attracted international buyers to visit Taiwan, where they can get a feel for Taiwan’s technological strength in the areas of information, communications, precision machinery, and machining. All kinds of supply chains, from controllers to manufacturing machinery, are concentrated within the relatively small space of our island, and buyers are greatly impressed by the fact that within only a day or two they can travel the length of Taiwan and find all the equipment they desire.

TIMTOS has become the world’s third largest machine tool exhibition.
Energy saving and carbon reduction
In pursuit of the goal of achieving net zero carbon emissions worldwide by 2050, Tommy Hsu says that machine tool companies across Taiwan have been working out solutions and applications to save energy and reduce carbon emissions in all aspects of manufacturing, from production design to energy management to production efficiency. In fact, these firms have already achieved much success in this regard.
For example, at TIMTOS 2023 the Victor Taichung Machinery Works displayed variable-frequency smart ball screws that can be used to implement oscillation cutting in place of high pressure cutting; this new technology can reduce electricity consumption by 58%.
Meanwhile, Hiwin Technologies Corporation promoted its underwater direct drive rotary table, which performs thermal analysis of the motor to save electricity and uses an algorithm to prevent hard shutdowns. In addition, with smart designs including intelligent ball screws and smart lubrication, the company provides sustainable solutions for environmental, social, and corporate governance (ESG) goals of low carbon emissions and low energy use.
Delta Electronics utilizes variable-frequency drives, smart electricity metering, and the collection and analysis of data on oils, electric power and humidity to implement energy management for its machinery, thereby achieving the effect of “green machine tools.”
Jywe Wen-yuh believes that TIMTOS 2023 shows there is already a trend toward making “intelligence” part of the standard configuration for individual machines. Taiwanese machine tool makers’ successful entree into EV and aerospace supply chains demonstrates their strength in resilient manufacturing, while the performance of component makers has been even more impressive. By rapidly reacting to the restructuring of global supply chains and taking up the challenge of reducing future carbon emissions, these companies are looking to occupy a leading position in the midst of globalization.
For more pictures, please click 《Smart Manufacturing, Green Industry—Trends in Taiwan’s Machine Tool Sector》