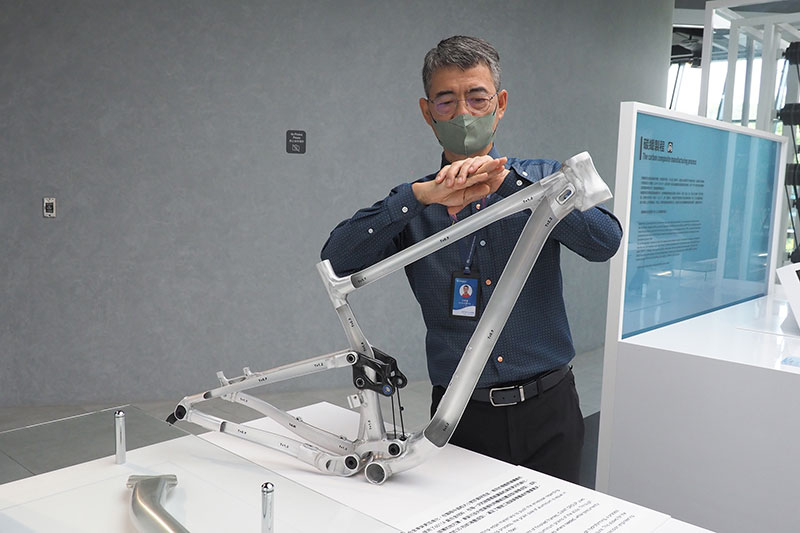
Howard Wang explains how Giant combined new frame technologies and materials to advance aluminum-alloy bike frames.
When you think about bicycles, what comes to mind? An adventurous BMX bike from your childhood? A YouBike pedaled around the streets of Taipei? A road bike used on weekend rides with friends? Whatever your personal experience of cycling, you know that Taiwan and bicycles go hand in hand.
Taiwan first imported bicycles for the wealthy while under Japanese rule. Our domestic bicycle industry began growing rapidly after the Second World War. In the decades since, Taiwan has become a top-tier global manufacturer of bikes and bicycle components, a host to R&D centers for major international brands, and the home of one of the world’s most important bicycle expos: Taipei Cycle.
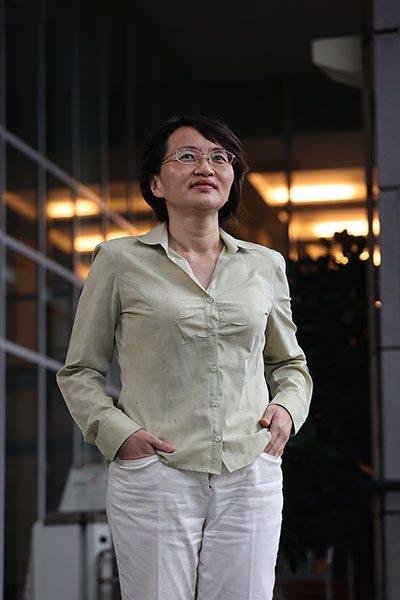
Michelle Hsieh says that the many hidden champions in Taiwan’s bicycle industry are behind its innumerable innovations.
Simple, but not
“Taiwan doesn’t have the world’s largest cycling population, but we manufacture components that the world’s ten largest high-end cycling brands use on their bikes. How did Taiwan manage that?” asks Howard Wang, operations director of the Giant Group’s Cycling Culture Museum, hoping to pique our curiosity.
Wang walks us through the history gallery on the first floor, explaining the global development of the bicycle. Invented in Europe more than 200 years ago, the bicycle’s steady improvement through the adoption of innovations such as pedals, brakes, chains, and diamond-shaped frames enabled it to transform human transportation.
When the 1970s oil crisis triggered a surge in the popularity of cycling in the US, Taiwanese businesses leapt at the opportunity. Present-day heavyweights Giant and Merida were founded in quick succession during this period, and component suppliers quickly grew up around them. Nowadays, Taiwan is home to more than 900 bicycle-industry companies clustered in the Taichung, Changhua, and Tainan areas.
As we wander through the museum’s exhibits, Wang shares cycling-industry milestones including Giant’s introduction of the “Red Samurai” BMX bike, the dream of many a young child in Taiwan and the US, and the company’s development of the much-emulated compact TCR frames, the lightness and stiffness of which gave riders a boost at the Tour de France. He also tells us about the materials innovations, from aluminum alloys to monocoque carbon-fiber frames, that have rewritten cycling history, and even goes into Taiwan’s world-renowned YouBike bikeshare program.
While bicycles may be simple devices, they utilize some less-than-simple technology. Once the world’s largest exporter of bicycles, Taiwan has transitioned from quantity to quality. With locally manufactured bikes now selling to international brands for an average of US$813 apiece, the value of our bicycle exports has grown exponentially.
Responding to global demand
How did Taiwan become a hub of high-end bicycle manufacturing? To find out, we spoke to Michelle Fei-yu Hsieh, an associate research fellow at Academia Sinica who studies industrial transformation in sectors such as the bicycle industry.
Hsieh says that when she was pursuing her PhD in 2002, China’s economic reform and opening policies had been in place for many years. With global manufacturers moving operations to China to take advantage of its cheap labor, conversations in Taiwan revolved around how the offshoring of production was hollowing out local industry. Though many people expected Taiwan’s bicycle industry to go into decline, industry figures explained to her that it was actually enjoying a golden age as the difficulties foreign companies were encountering developing products in China were bringing them back to Taiwan.
Not all of the bikes made in Taiwan in the 1970s were up to standard. Their uneven quality caused some customers to reject shipments outright. Public entities like the Metal Industries R&D Center and the Cycling and Health Tech Industry R&D Center stepped in to help local firms improve their manufacturing processes, standardize products, and upgrade quality control. According to Hsieh: “Quality inspections and standardization were important because they created technical capabilities, which enabled the rapid development of Taiwan’s components industry.”
The emergence of mountain biking represented another turning point for the industry. Mountain bikes brought variability to the conventional diamond frame. They also changed frame construction. Hsieh explains that traditionally, frame tubes were joined using lugs and brazing. If a bike maker wanted to adjust the angles of a frame, it would need to order new lugs, which in turn would require new dies. That difficulty encouraged the building of standardized, mass-produced bicycles.
Mountain biking, which became popular in the United States in the 1980s, involves riding on forest trails and therefore requires a more robust bike frame. This led US manufacturers to begin using tungsten inert gas (TIG) welding to build the frames, which eliminated the need for lugs, reduced costs and production time, and enabled low-cost experimentation. Meanwhile, Taiwan’s experience manufacturing BMX bikes for export had cultivated a pool of skilled arc welders who began training themselves to do TIG welding. Their skills enabled Taiwanese firms to accept orders from US companies and quickly respond to market demand. “When mountain biking took off, Taiwan seized the opportunity, laying the foundation for its emergence as the world’s cycle-making king.”
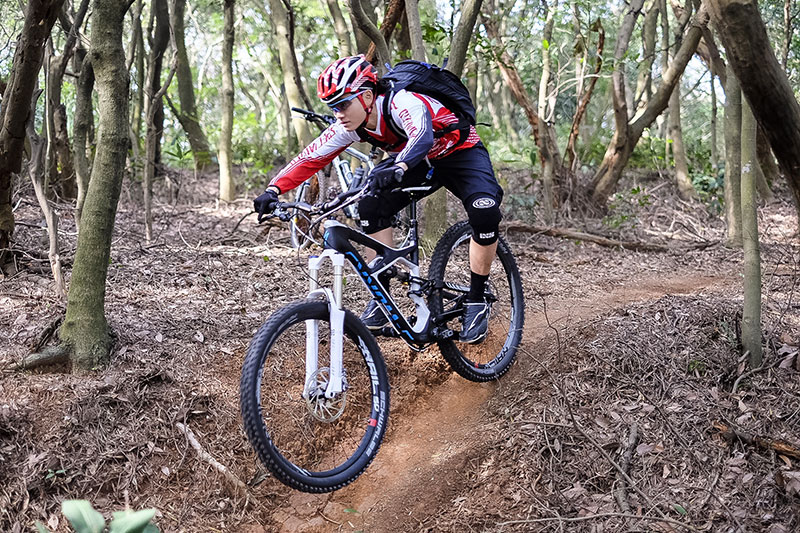
Mountain biking required changes to frame assembly techniques and encouraged component manufacturers to innovate. The resulting move away from standardized components led to explosive growth in customized parts. (photo by Kent Chuang)
Cooperative and competitive
Taiwan’s TIG welding breakthrough encouraged further innovation at bicycle component makers, resulting in a rapid shift from standardized components to more customized parts, and making Taiwanese component makers aware of the market potential for these products.
Hsieh says that Taiwan’s distributed production system and its orientation around small and medium-sized enterprises (SMEs) were key characteristics of the island’s postwar development. But these SMEs’ relative lack of resources and manpower and their tendency to keep to their own market niches left them with very few opportunities to conduct their own R&D, which was an obstacle to upgrading their businesses. Fortunately, Taiwan’s bicycle industry developed a slightly different model: as exporters operating in niche markets, component makers came to realize that their competitors were not the companies next door, but those overseas. In addition, the openness of the local bicycle manufacturing network enabled component makers to be flexible in sourcing materials, to supply multiple bicycle makers at the same time, and to sell products into other industries.
We often think of “innovations” as involving game-changing moments like Steve Jobs’ introduction of the iPhone, but Hsieh points out that the smaller, more mundane breakthroughs in technology and manufacturing processes that occur within companies on a regular basis are also innovations. “Taiwan’s open production network encourages the free flow of information and best practices. It allows companies to quickly find solutions to problems and facilitate technological innovations by reconfiguring production processes.”
A high-end manufacturing hub
Other innovative ideas have trickled in from neighboring industries, such as the machine tool and metal manufacturing sectors, or even via cooperation with materials suppliers.
These Taiwanese businesses have a horizontal relationship. Everyone knows everyone else and participates in warm and lively exchanges. If someone has an idea, they first talk to others about it, and then determine whether there are opportunities for cooperation. “Everyone in this cluster is willing to try out new ideas and innovations, which results in many of these ideas getting implemented. Firms actually like to take on these kinds of projects because they find the challenges interesting.” The business environment draws companies seeking to put innovations into practice to Taiwan to look for resources within the cluster, which has contributed to Taiwan’s transformation into a global hub for high-end bicycle manufacturing.
Local manufacturers have also responded quickly to the recent market demand for electrically assisted bicycles. Hsieh says that e-bikes require different frame tubes than unpowered bikes because they have to accommodate a battery and other components. E-bike frames must also be drilled with holes for wiring, which is time consuming on a CNC machine. But Taiwanese manufacturers have an edge in building such frames because they already have the necessary processes and equipment in place. While foreign companies control the technologies underlying e-bike propulsion systems, they still have to work hand in hand with Taiwan’s frame makers and component makers to bring their e-bikes to market. In a tacit acknowledgement of this reality, Bosch, the world’s dominant producer of e-bike motors, has located its Asia–Pacific headquarters for e-bike systems in Taichung.
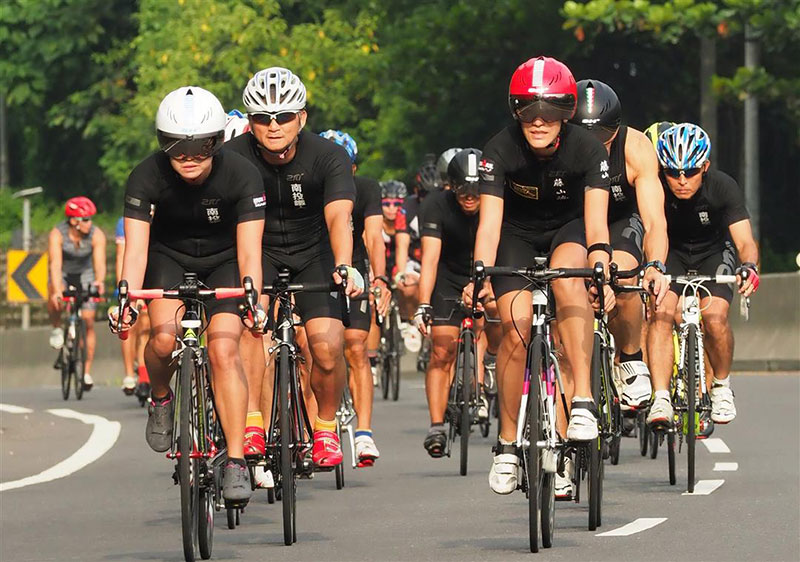
Cycling is on the rise in Taiwan, where groups of riders are becoming a common sight on holidays.
Progress is a group effort
A key moment in the development of Taiwan’s bicycle industry came in 2003, when local heavyweights Giant and Merida formed their own version of the A-Team. A joint effort to upgrade the local industry while keeping its roots in Taiwan, the program had each company encourage the transformation its component suppliers.
Wang mentions that the component makers, who were then exporting 7–8 million units each, really didn’t want to open up their factories to one another out of fear that others would learn their particular trade secrets. But they eventually realized that each of them had areas in which they excelled, and that comparing notes enabled them all to improve. The companies subsequently transformed into “high-mix, low-volume” producers of smaller quantities of varied high-end parts and high-value-added products. Their success is a testament to what A-Team members told Hsieh at the time: “Our goal is not to integrate the supply chain, but to learn.”
When the A-Team finished its mission in 2016, Hsieh recalls asking Giant why it had invited its competitor to be part of the effort. The company told her: “It’s a big market. We wouldn’t have been able to persuade suppliers to participate in the upgrades by ourselves.” It required a group effort to succeed.
“Taiwan’s bicycle story isn’t one of individual companies, but of the whole production chain. There were so many hidden champions supporting these innovations, and the innovations themselves were all interconnected. They grew out of many resources and many technologies coming together at the right time and place. All of those things had to be in place for Taiwan’s bicycle industry to blossom,” concludes Hsieh.
For more pictures, please click 《Spinning Wheels: How Taiwan Became a Hub for High-End Bicycle Manufacturing》